Archives: Rashmi Products
Superior Portland Slag Cement
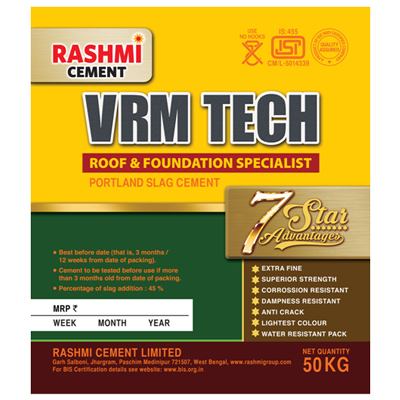
Superior Portland Slag Cement is commonly known as PSC and is a special blended cement, produced in state-of-the-art manufacturing facilities with superior quality slag (a non-metallic product comprising glass with silicates and alumina-silicates of lime), produced at our steel manufacturing plant. To ensure that the Portland Slag Cement delivered to our customers is exceptionally strong and durable, our engineers do constant quality monitoring, adhering to ISO-certified systems and procedures. It is one of our most popular cement products because it is environment-friendly and offers an array of benefits such as great compressive strength, low cracking risk, and resistance to alkali-silica reaction and Chloride & Sulphate attacks. PSC can be used in all types of residential, commercial, and industrial construction projects.
Ordinary Portland Cement
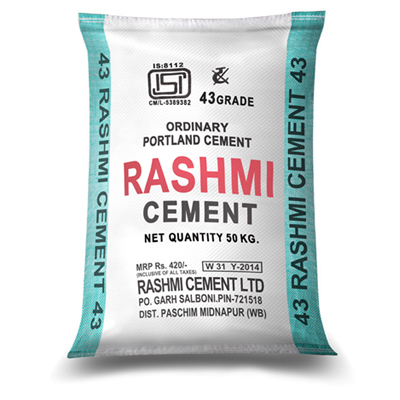
Ordinary Portland Cement is commonly known as OPC and can be used in concrete construction projects that do not involve exposure to sulphates either in the soil or groundwater. Concrete produced from Ordinary Portland Cement is quite common and used in a wide range of applications such as civil engineering works, plastering mortar, general-purpose buildings, and so on. At Rashmi Cement, our engineers abide by the most advanced manufacturing standards in the production of OPC. Right from choosing the best calcareous and argillaceous materials to monitoring their right proportion – they ensure that the quality of the manufactured Ordinary Portland Cement caters to the requirements of the specified construction works.
Supremo
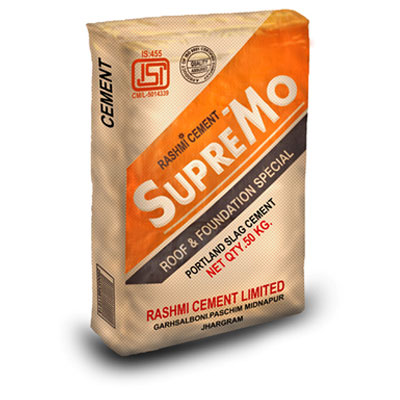
Supremo is a cement product specially manufactured for building stronger and longer-lasting roofs and foundations. Made from the finest quality of limestone and state-of-the-art technology deployed in the cement plant, it has all the required properties that make it stronger, denser, and leakproof, resulting in strengthening of the roof and foundation. In comparison to other types of cement available in the market, it is the most suited for all types of critical load-bearing applications like roofings, foundations, beams, and columns. The usage of Rashmi Cement Supremo protects you from common roofing and foundation repair issues caused due to rain, humidity, and many other factors.
Portland Pozzolana Cement
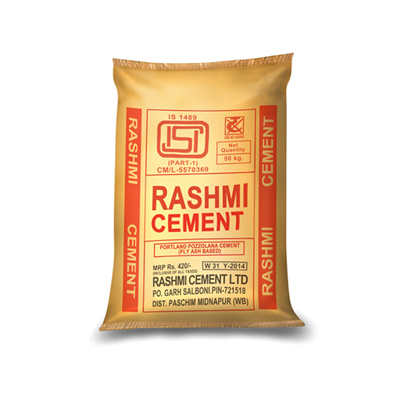
Portland Pozzolana Cement is commonly known as PPC cement and is manufactured, using Fly ash as the main constituent which is obtained from thermal power plants. In comparison to Ordinary Portland Cement (OPC), Fly ash-based Portland Pozzolana Cement is much better as it has a long-term strength and makes concrete more water-repellent and dense. Considering the fact that it is highly resistant to sulphates, produces less heat of hydration, is resistant to expansion, and cheap and affordable, makes it is a popular choice. It is ideal for a variety of construction projects such as hydraulic structures mass concreting works, marine structures masonry mortars, and many more.
Dredging
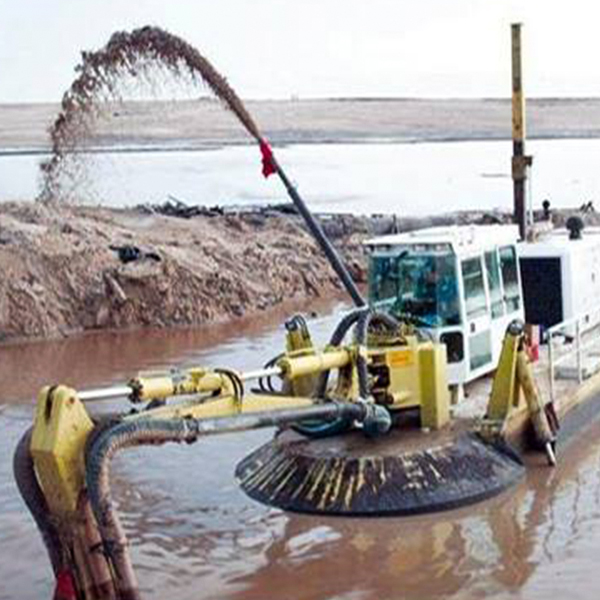
We offer a wide range of dredging services that involve removing sedimentation from dams, ponds, lakes, rivers, harbors, beaches and other water bodies. Our team consists of some of the most experienced professionals of the dredging industry who provide full turnkey service from consultation and planning to execution and assessment. We involve clients at every step of the dredging process to maintain complete transparency in the service. Till date, we have done dredging work for clients in different domains.
Billet
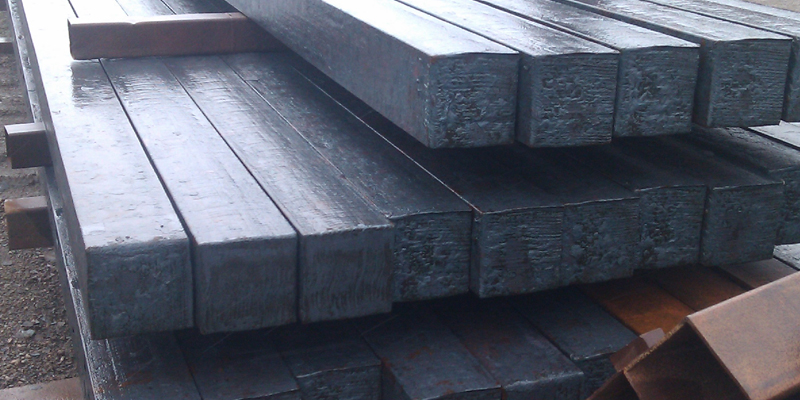
Rashmi Metaliks is one of the largest players in Billets in Eastern India. We came up with our own Steel Melting Shop in 2009, producing billets at a capacity of 1.6MTPA. Applying the latest innovations and state-of-the-art technology in the manufacturing process, we ensure that the billets produced are accurate and meet industrial standards. Right from melting the sponge iron at the right temperature to adding corrosion-resistant alloys to the billets – highly trained personnel monitor every aspect. At the end of the process, cast billets are sent to the laboratory for a stringent checking of their properties and forwarded to the Quality Control Department, which ensures they comply with IS: 2830 & 2831.
Features:
- Dimensionally correct
- Tremendous tensile strength
- High temperature tolerant
- Extreme pressure tolerant
- Corrosion resistant
- Used in varied industrial and commercial sectors
Sponge Iron
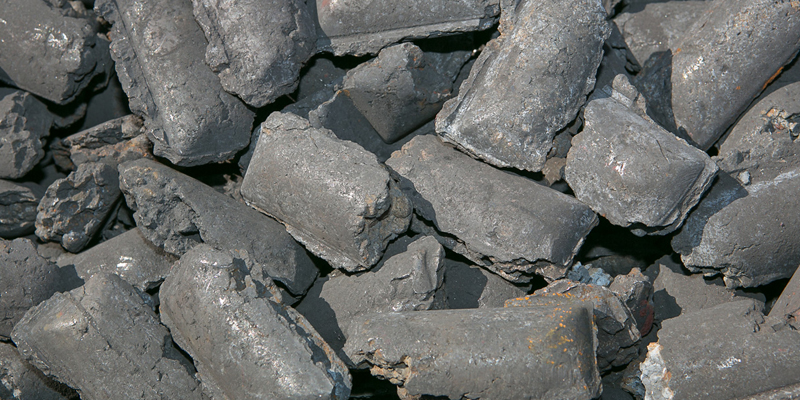
Rashmi Group is the largest manufacturer of Sponge Iron in Jhargram& Kharagpur, West Bengal, India with a capacity of 3.19MTPA. We produce high-quality Sponge Iron that meets the industry standards.
The production process followed at Rashmi Group makes the Sponge Iron unique and superior than its competitors. Iron ore (Red Hematite) is extracted from the mines and taken to the DirectReduced Iron (DRI) Plant where it is charged with different sizes of Coal (Carbon) by conveyors from different stock houses into the Rotary Kiln.
Physical factors like Temperature & Air volume in the compartment of the Kiln determine the course of the reduction reaction, known as the ‘BURWAD’ reaction. Reactants eventually get reduced and Sponge Iron mixed with Charcoal is obtained. A magnetic Separator is used to extract the Sponge Iron. Abiding by strict quality standards, a sample of Sponge Iron is taken for testing, after which grades are assigned.
Pellet
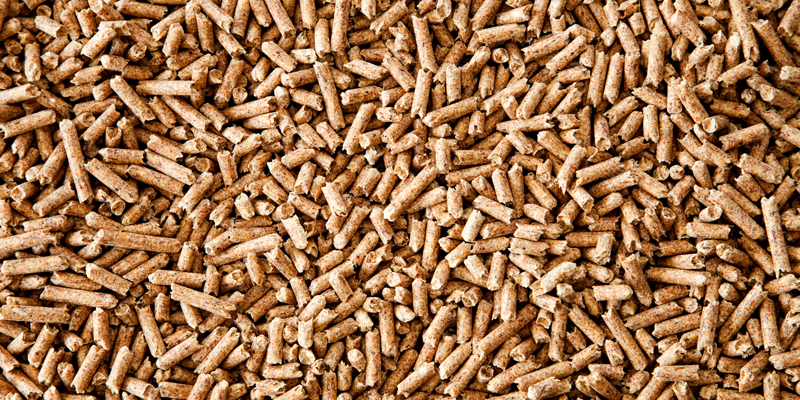
Rashmi Group is the first to set up a Pellet Plant in West Bengal. Since the time the commercial production of pellets commenced, Rashmi Metaliks has witnessed a meteoric growth. It is a result of this fact that today we are one of the largest players in the manufacturing of Iron Ore Pellet in eastern India. The company’s plant produces different grades of pellets and has a capacity of 9MTPA.
Advantages of Iron Ore Pellet :
- Superior to iron ore lumps
- Not vulnerable to degradation due to being corrosion resistant
- Helps in faster reduction and higher metalization rate
Sinter
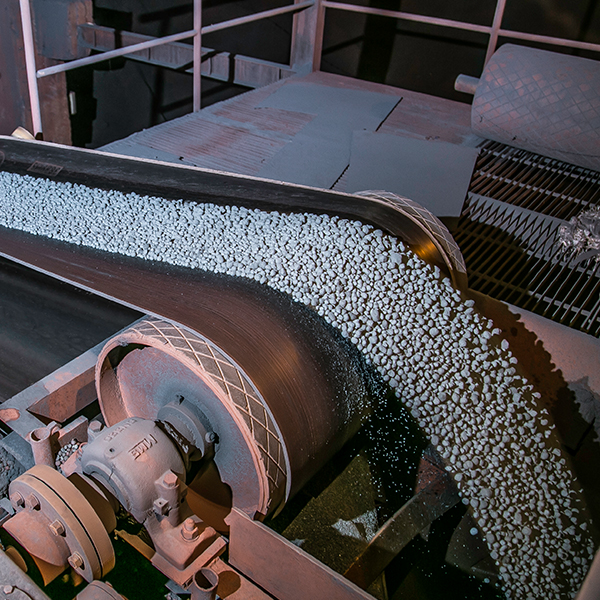
Iron Ore is the most important raw material needed to produce steel. However, it cannot be used directly in the blast furnace. That is why sinter is created that helps convert iron into steel. Rashmi Metaliks has its own Sinter Plant set up at 2007 to have complete control over the quality of materials used in the steel production process.
In our Sinter Plant, a mixture of fine-grained iron ore, ferriferous recuperation materials, and fluxes is baked on a conveyor belt which is fueled by gases of the blast furnace. The mixture is heated using the burners on top. As the grid conveyor belt moves, the air is sucked away from the mixture. Combustion happens through the entire layer where the temperature rises between 1300 – 1480o centigrade.
At the end of the burning process, sinter cake is discharged on a crash-deck, crushed, cooled by forced air, and size-screened. Sinter which is a small, irregular nodule of iron mixed with small amounts of other minerals has the perfect chemical composition and grain size to be charged in the blast furnace.